Optimizing Bulk Bag Filler Offers Significant Rewards
An expert integrator reveals best practice strategies to increase productivity and profit by upgrading critical bulk bag filling equipment.
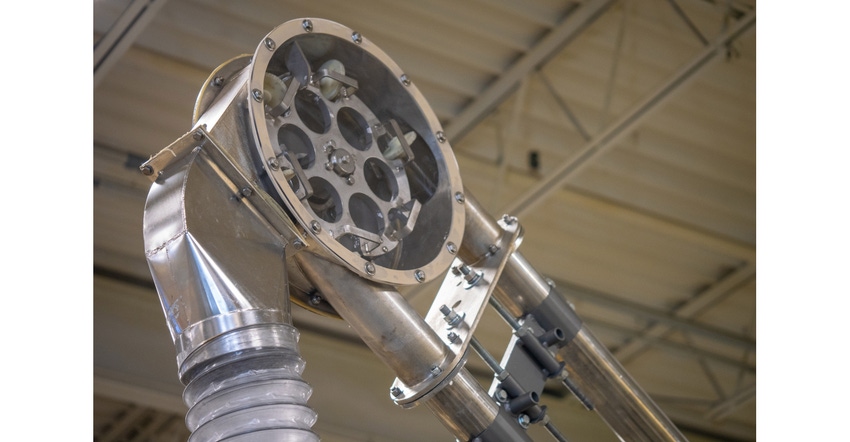
Bulk bag filling stations play a pivotal role in ingredient packaging, enhancing the speed and efficiency of the packing procedure. With an array of models available, these systems range from hand-operated setups to semi-automated units. Semi-automated fillers can significantly increase productivity and the bagging rate by automatically introducing a pallet to the machine and removing filled bags, reducing the time required to manually handle every pallet and filled bag.
We examined the benefits of upgrading bulk bag filling equipment and discussed some options to cost-effectively optimize the process with industry expert Don Mackrill of Automated Handling Solutions (AHS), which provides engineering solutions that incorporate specialty conveyor, material handling, and automation equipment technologies.
Q: How can Powder & Bulk Solids readers benefit from improving their bulk bag filling equipment?
A: While many systems enhance the speed of bagging operations, there is a continual opportunity to refine and improve efficiency and output. By integrating advanced bulk bag filling equipment, companies can realize substantial gains in productivity by increasing the number of bags filled per hour, allowing more product to fit in existing bags, and even facilitating a transition to smaller bag sizes.
These types of upgrades can substantially reduce operating costs, increase production throughput, reduce shipping costs, and even help processors recover lost revenue.
Q: I understand that improving weighing accuracy is one way to help recover lost revenue. Can you tell us more about this?
A: Products sold by weight must be filled to the advertised weight. To avoid the possibility of underfilling, manufacturers frequently opt to fill packages more than necessary, which results in lost revenue that can accumulate over time. Inconsistent fill weights only increase potential losses.
Processors don’t get paid for the extra pounds they overfill the bag. If they can improve the weighing accuracy, they are not giving away as much free product. Switching to a bulk bag filler that offers precise weighing accuracy can effectively resolve this issue.
If you can improve the weighing accuracy of your current bulk weighing system from +/-5 lb to +/-1 lb, you are no longer overfilling as much. From an accounting perspective, that is recovered revenue that goes right to the bottom line. When the bagging rate exceeds 30–35 bags/hr, pre-weighing the material in a hopper above the filler should also be considered.
Pre-weighing the “shot” of material while a bag is being densified and removed from the system and the next bag is rigged, significantly increases the bagging rate. Some bulk bag filler systems are capable of filling more than 40 bags/hr if the material is pre-weighed.
To further enhance the precision of weighing, it is important to consistently fill hoppers with equal amounts of material and align this process with the pace of bagging operations. Even minor factors such as the volume of material in the silo that feeds the hopper can upset the timing. As the weight of the material in the silo decreases, so does the flow rate, which makes it difficult to predict how fast product is going to come out. If you can consistently match the conveying rate into the hopper with the bagging rate, then you can dial in a very tight weighing accuracy.
Q: How important is compacting material more efficiently in bulk bag filling equipment? What role does powder bulk density play in this?
A: Upgrading bulk bag filling equipment to a more efficient system that can compact or densify the material in each bag offers significant cost-saving opportunities. One effective strategy for reducing packaging costs is to efficiently increase the density of the product in each bag. By doing so, it may be possible to purchase smaller bulk bags while still shipping the same quantity of product.
On the other hand, for powders with bulk density less than 25–30 lb/cu ft, it may be possible to increase the product capacity within the existing bag size. This allows food and beverage processors to consistently approach the maximum weight restrictions permitted on truck trailers and avoid additional shipping expenses incurred when the weight falls below the limit.
Maximizing the amount of product in existing packaging dimensions can lead to increased production efficiency, potentially reducing the time required to operate the production line to achieve the desired quantity of goods. Any surplus capacity can be used to accommodate increased demand and support the sale of additional products.
Q: Can powder densification lead to even greater savings?
A: Yes, enhancing material densification leads to a “ripple effect” of savings.
You’ll weigh out every trailer and over time fewer trailers will be required to transport the total product weight within a specific timeframe. Additionally, the increased capacity of each bulk bag results in filling fewer bags, thereby reducing packaging costs.
Another benefit is improved bag stability. Some dry materials will entrap or entrain air between the particles more than others, and those that do require more vibration or densification to drive out the air between the particles. When that is not the case, the bulk bags can become unstable and tip and fall during transport, handling, or storage. This can put operators at risk of injury, damage product, and increase operational costs.
Unstable bulk bags can topple off a pallet while being moved by forklift or can lean or slump over in a truck trailer as it bounces down the road, making unloading difficult and even posing a safety hazard. The primary purpose of a bulk bag filling machine is to produce a safe and stable bulk bag.
To improve bulk bag stability and safety, some equipment is specifically designed to compact difficult fill material such as powders, granules, or flakes that are easily aerated. One bulk bag filler, for example, utilizes patented cone table densification that deaerates the material with a flattened angle of repose, resulting in a very safe and stable bag.
The speed at which powders are compacted in the bag also impacts productivity. If it takes you 20 minutes to vibrate through the pallet into the bag with your current machine to the point where you can safely handle it, replacing it with a machine that can do the same in two minutes dramatically improves productivity.
Q: Are there other ways to streamline the bulk bag filling process and what considerations should be made?
A: Increasing the productivity of bulk bag fillers may require an upgrade or redesign of the conveyor system that transports products to the fillers. However, it can be difficult to select the optimal mechanical conveyor system. This is the case when purchasers are relatively uninformed about the specific attributes and advantages unique to each conveyor type available on the market.
The most critical aspect to consider is the type of product that the processor is trying to convey. Issues such as product flowability, abrasiveness and cohesiveness should always be considered, whereas product degradation or the need to maintain a blend may be key aspects to consider in some applications.
For food-grade applications, hygiene specifications and the ability to clean-in-place are important considerations.
Q: What types of conveyors generally meet these requirements? What aspects should be considered, and who can help with this?
A: There are several categories of enclosed conveyors that meet these requirements, including aero mechanical, flexible screw, and tubular cable drag designs.
Conveyors are almost always part of an integrated system with fillers because as soon as you get material in or out of the bag, you need to take it somewhere. We want to do that in a fully enclosed environment so that we’re not letting dust out into the plant, not losing product, and not leaving the conveyor open to humidity or rain if some of the conveyor is outdoors.
Still, every material handling scenario is unique. Dealing with difficult powders or delicate, sticky products presents its own set of challenges.
To resolve these issues, powder and bulk solids processors--particularly those in the food industry--can benefit from the guidance of expert powder conveying integrators that have implemented various equipment types in complex applications over decades. An experienced integrator can not only help a processor select the best type of conveyor for their application but also optimize it for their specific type of food and process.
Tubular cable drag conveyors are going to be extremely gentle. Aero mechanical conveyors are a little harder on product, but extremely quick. Flexible screw conveyors are very cost effective in getting product from point A to point B.
To ensure optimal results, we recommend rigorous testing of powders, including assessment and analysis of the materials’ flow characteristics.
For more information, contact Spiroflow Systems at 704-215-2624 or [email protected], or visit www.spiroflow.com.
About the Author(s)
You May Also Like